This project explored end effector designs to determine the most effective way to grip pill bottles ranging from 35 mm to 135 mm in diameter. After testing various concepts, including suction-only mechanisms, a parallel gripper was selected as the most suitable solution due to its adaptability, grip security, and scalability. Two primary parallel gripper concepts were developed and tested: a linkage-driven gripper and a lead screw-driven gripper.
The linkage gripper used a stepper motor with a coupler featuring two perpendicular prongs. As the motor rotated, the prongs moved in opposite directions. Curved linkages were connected from each prong to individual linear rail carriages, allowing for symmetrical motion of the gripper claws. The curved shape of the linkages was optimized to maximize travel and fold around the coupler, maintaining a compact form factor. A constant-force spring was added between the claws to create a normally closed position, eliminating the need for continuous motor power to maintain grip. While this design demonstrated smooth motion and efficient energy usage, it had a limited gripping range of 20 mm to 115 mm and struggled to securely hold heavier pill bottles, falling short of the application's requirements.
The second design, a lead screw-driven gripper, consisted of one fixed claw and one movable claw mounted on two linear rail carriages for smooth, stable motion. The movable claw was actuated by a horizontally mounted, single-start lead screw driven by a stepper motor. This setup offered strong linear force and a mechanical self-locking effect. The gripper's default position was open, and it closed around a pill bottle until resistance was detected—signaling a firm grasp—at which point the motor power was cut. This design proved to be both robust and reliable, with a functional range of 20 mm to 150 mm, making it well-suited for securely gripping a wide variety of pill bottle sizes.
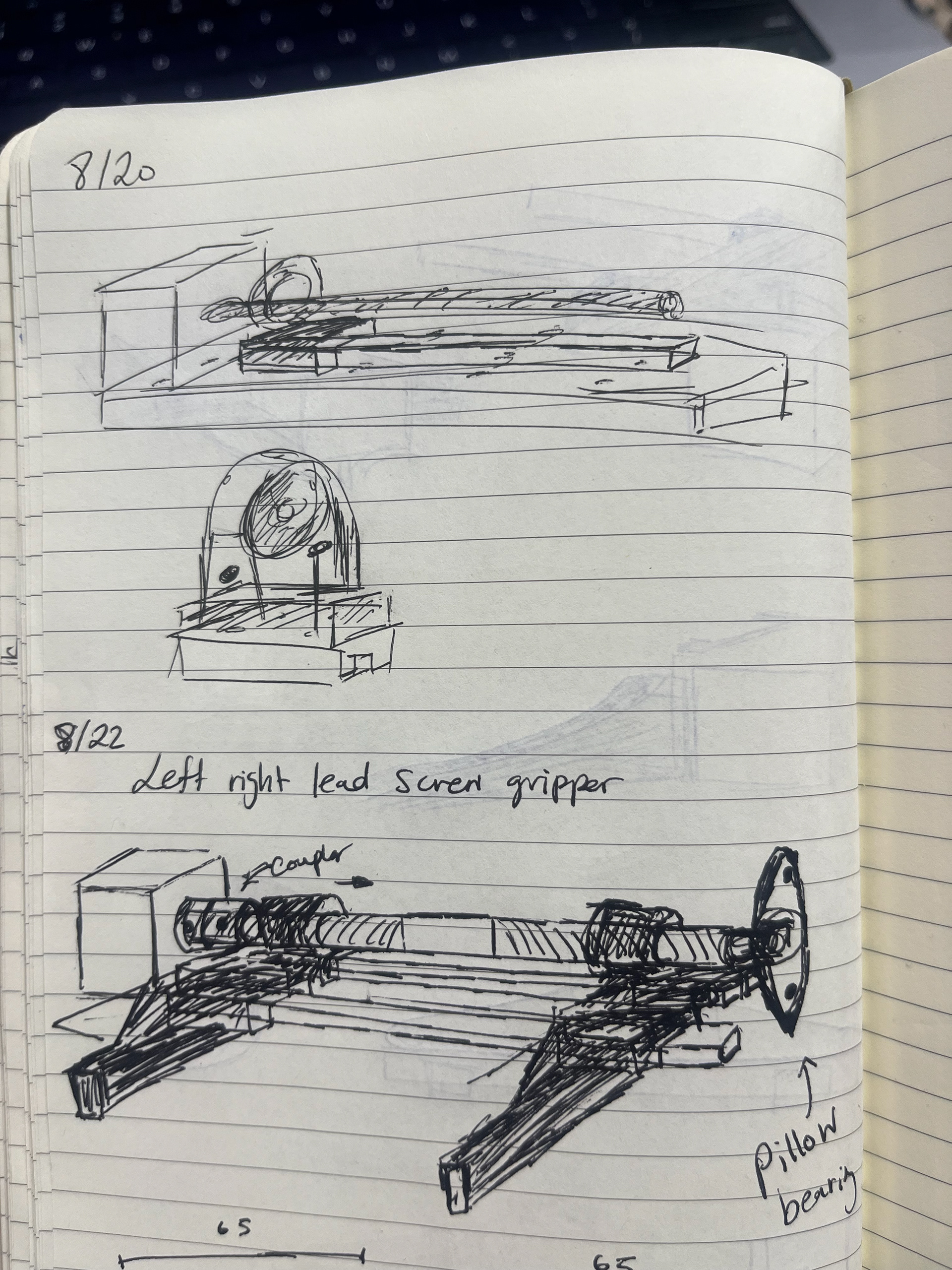
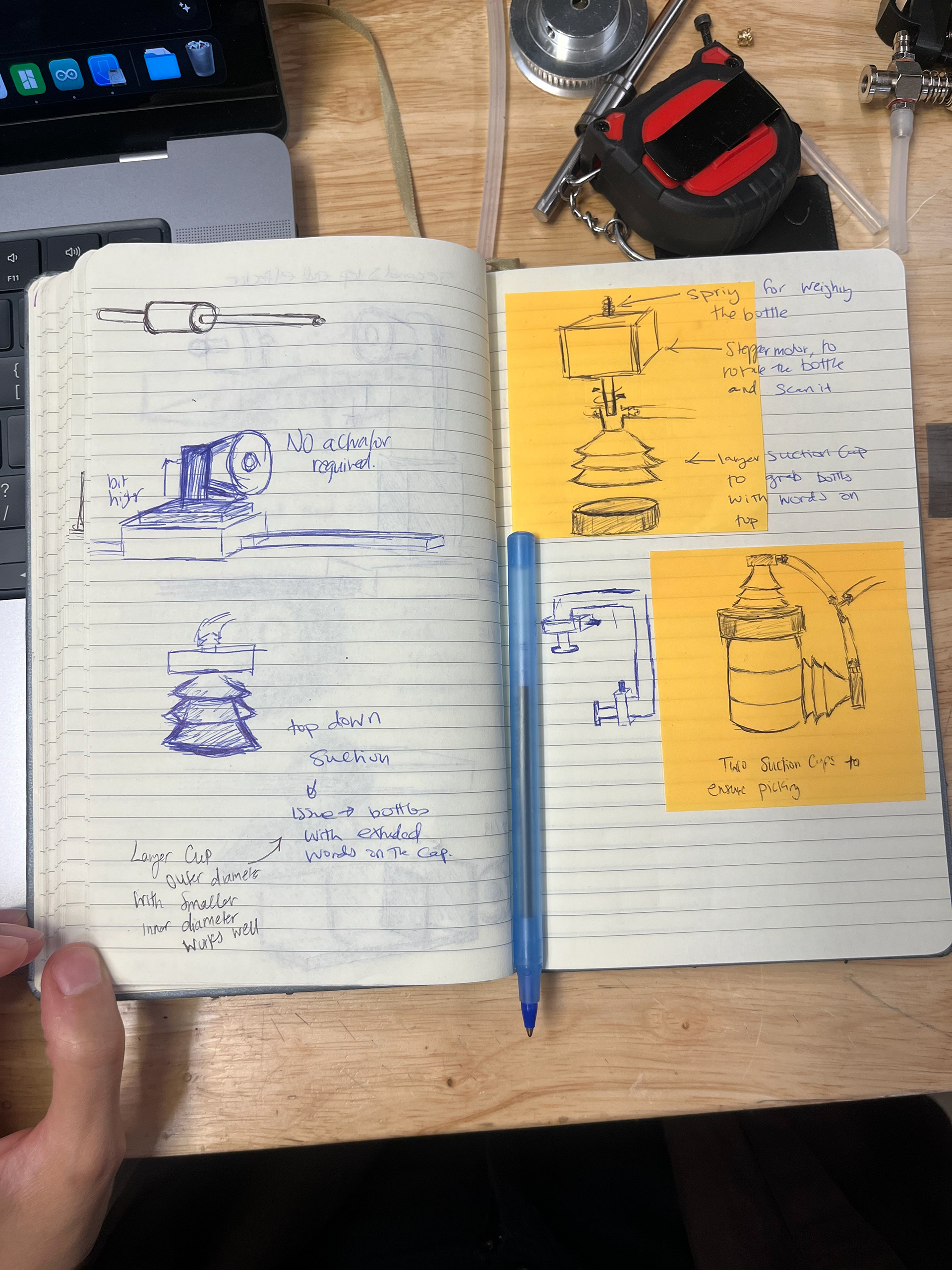
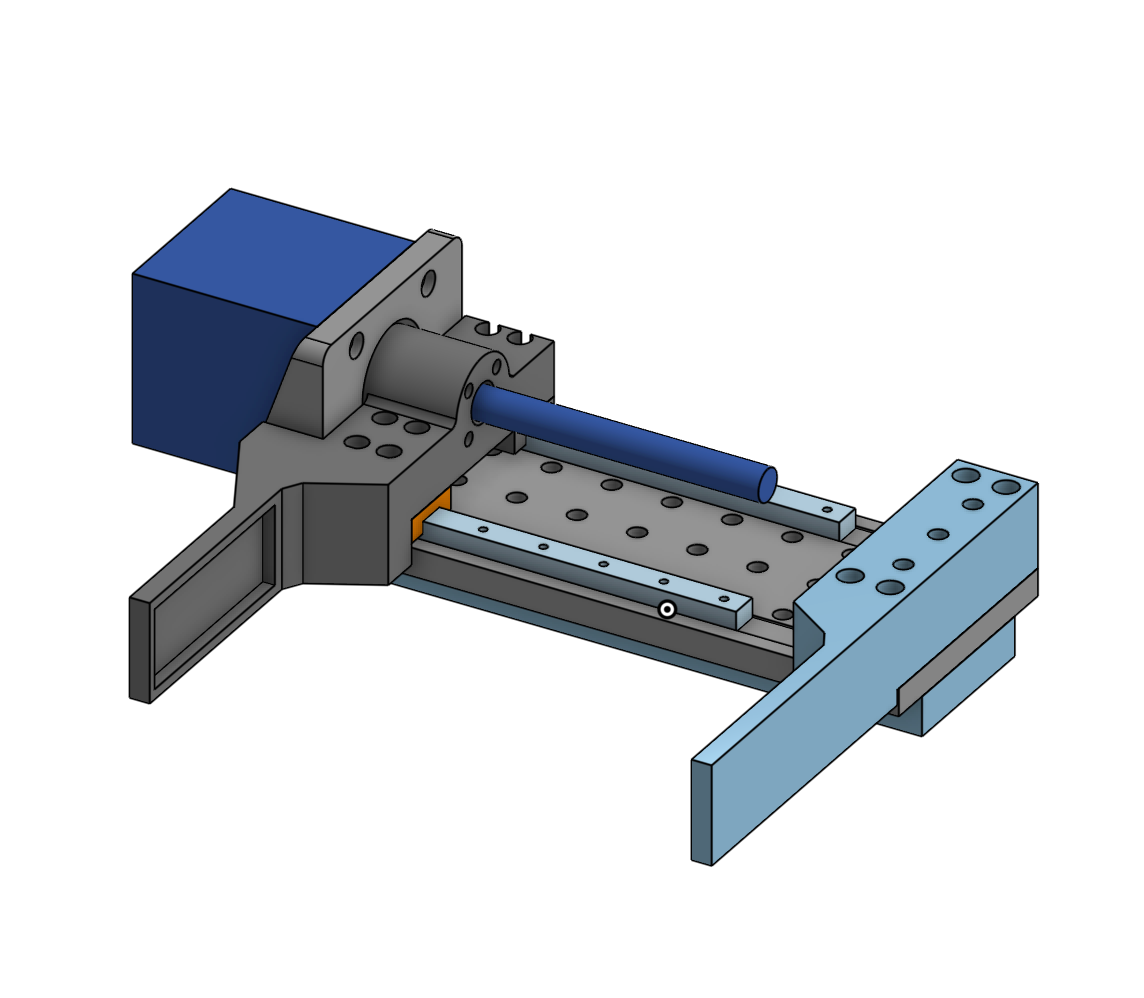
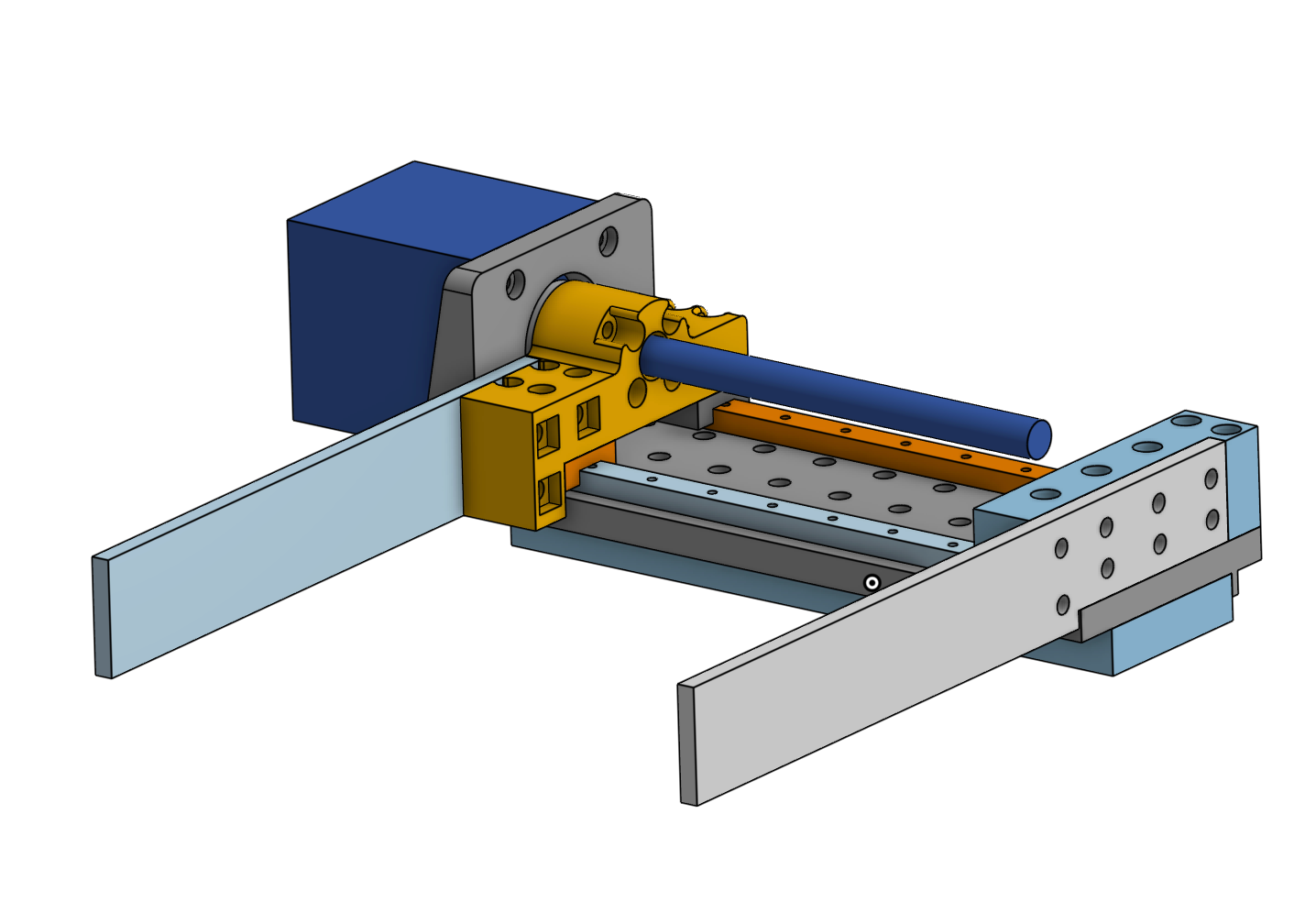
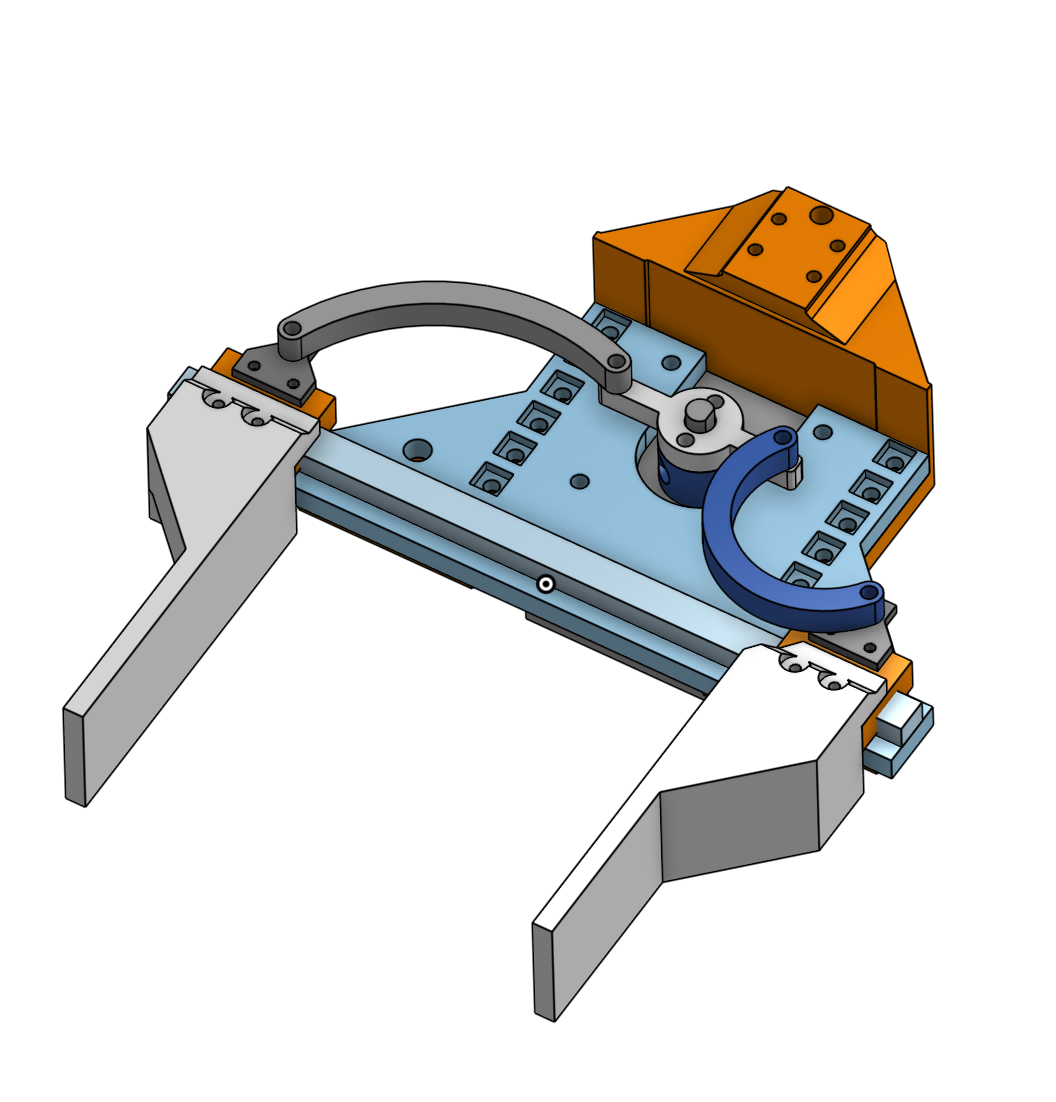
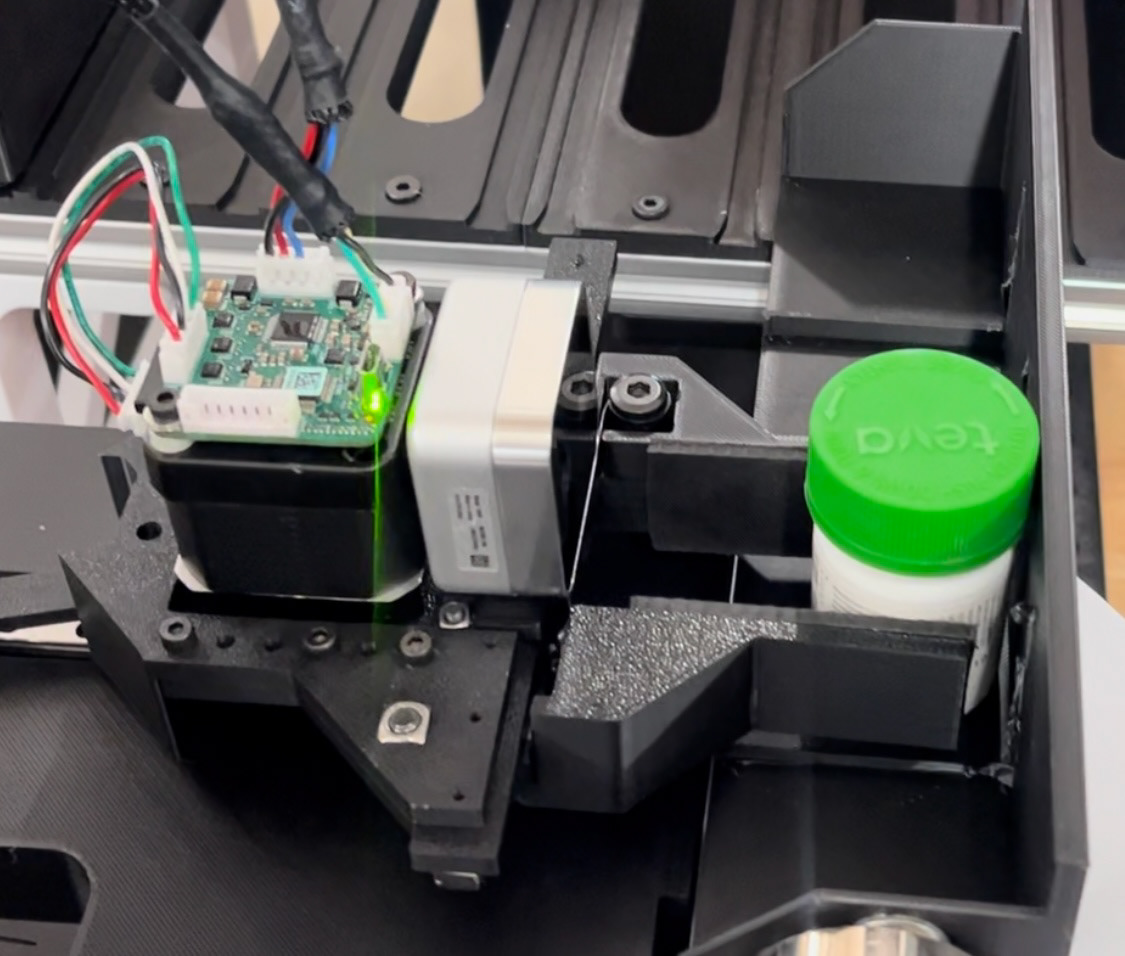
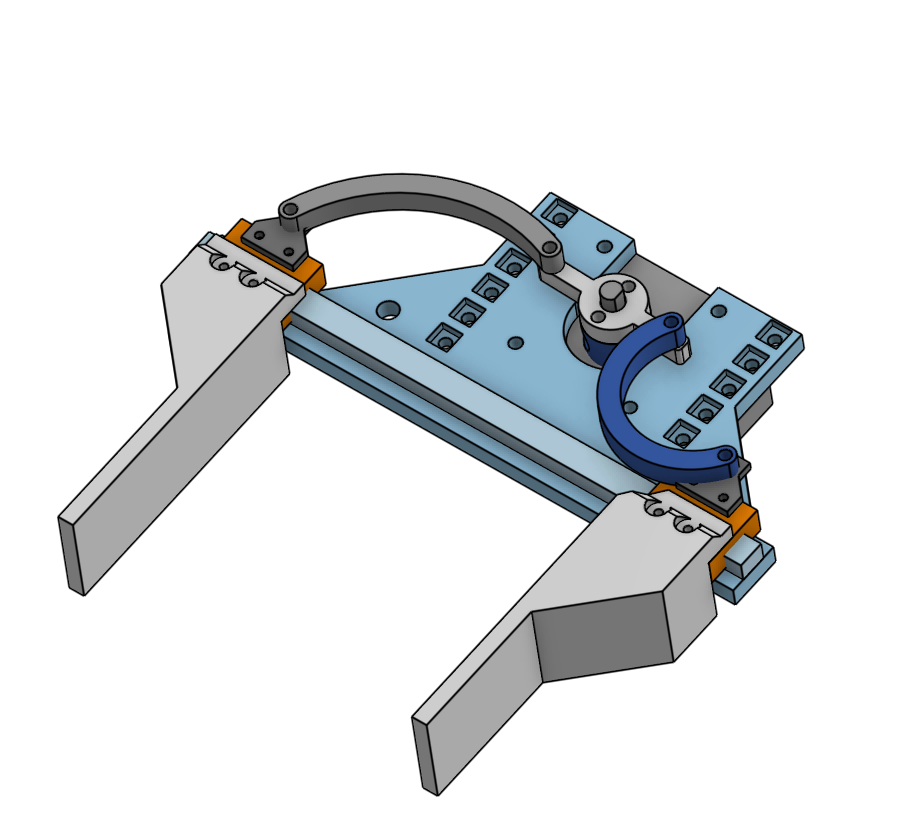
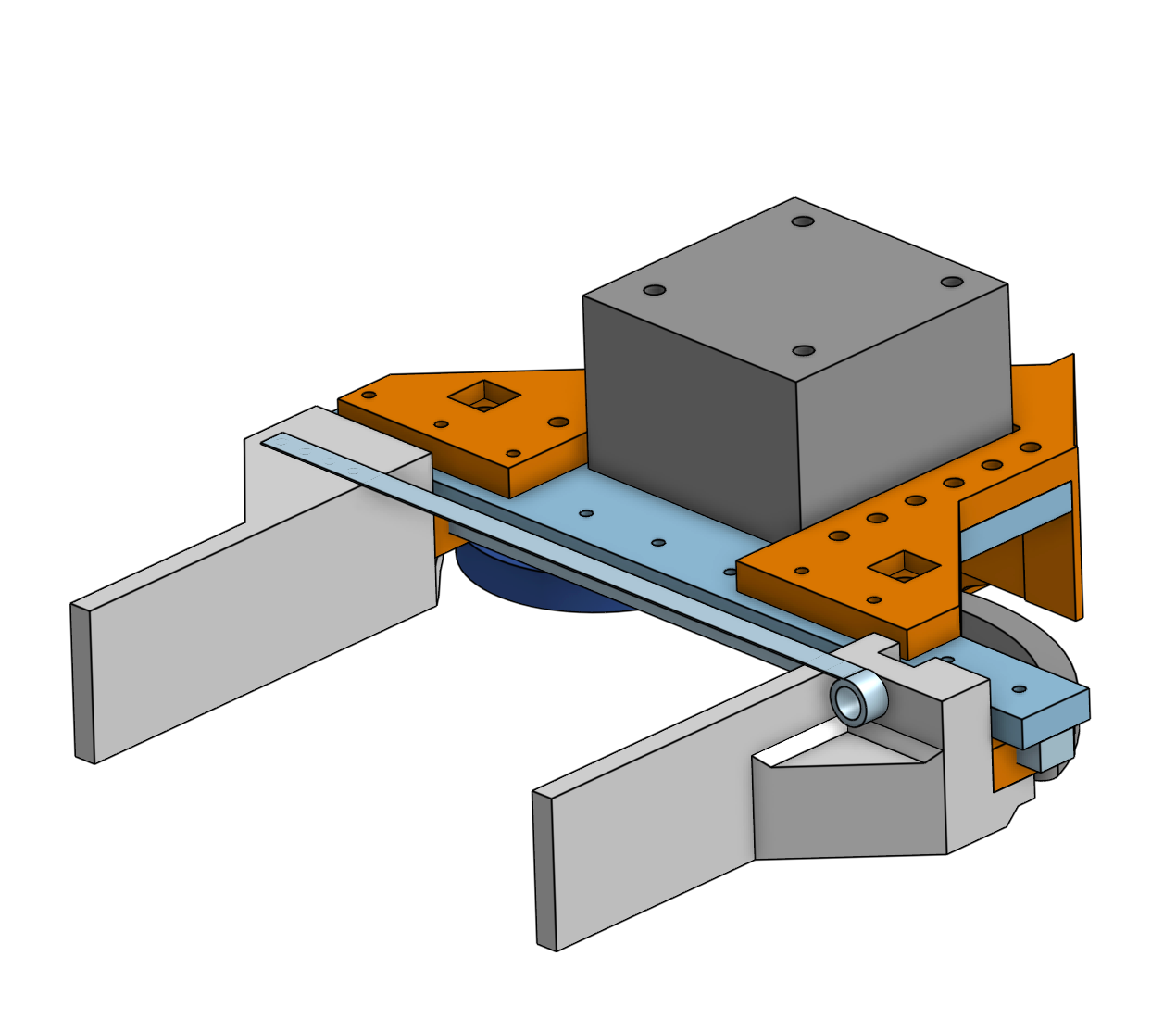
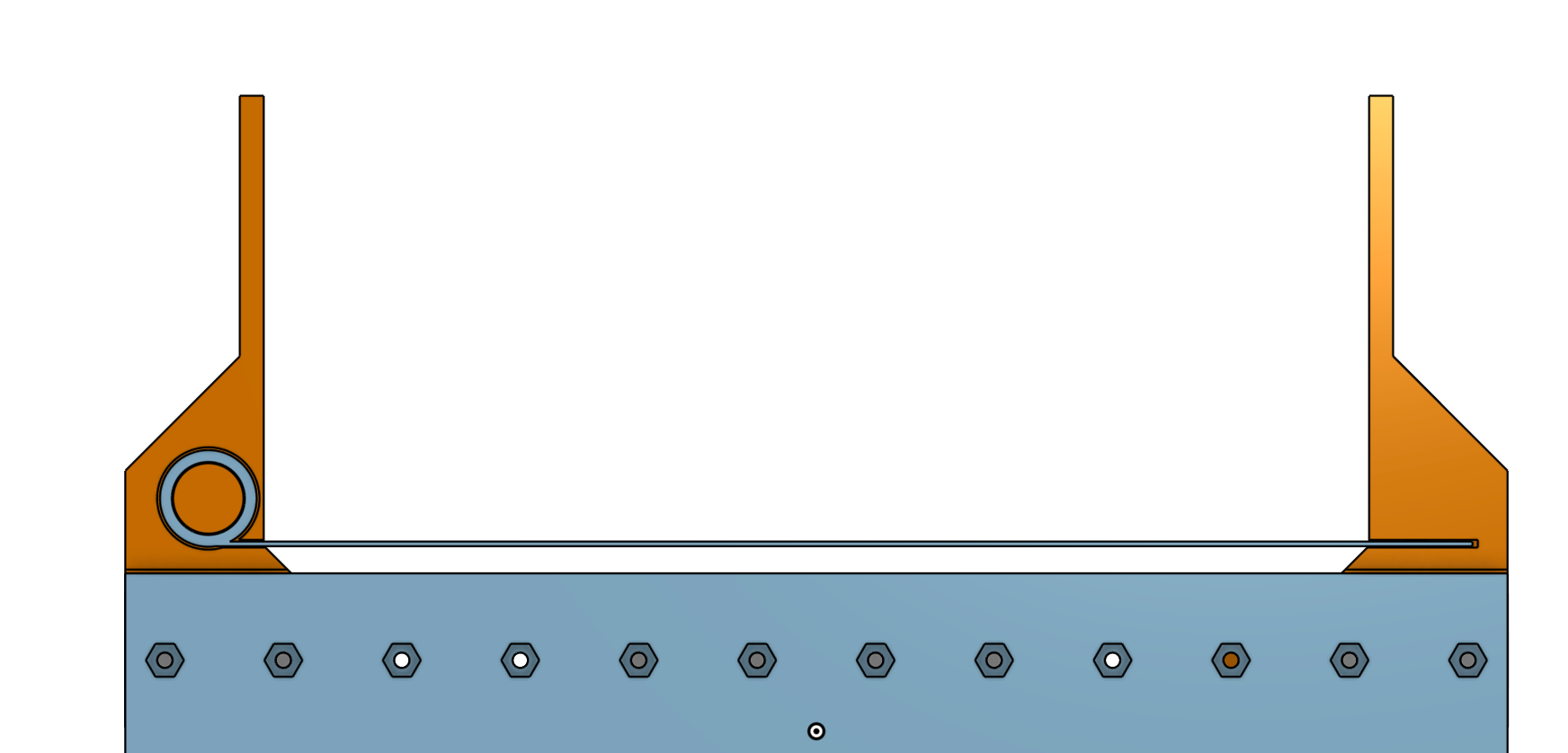
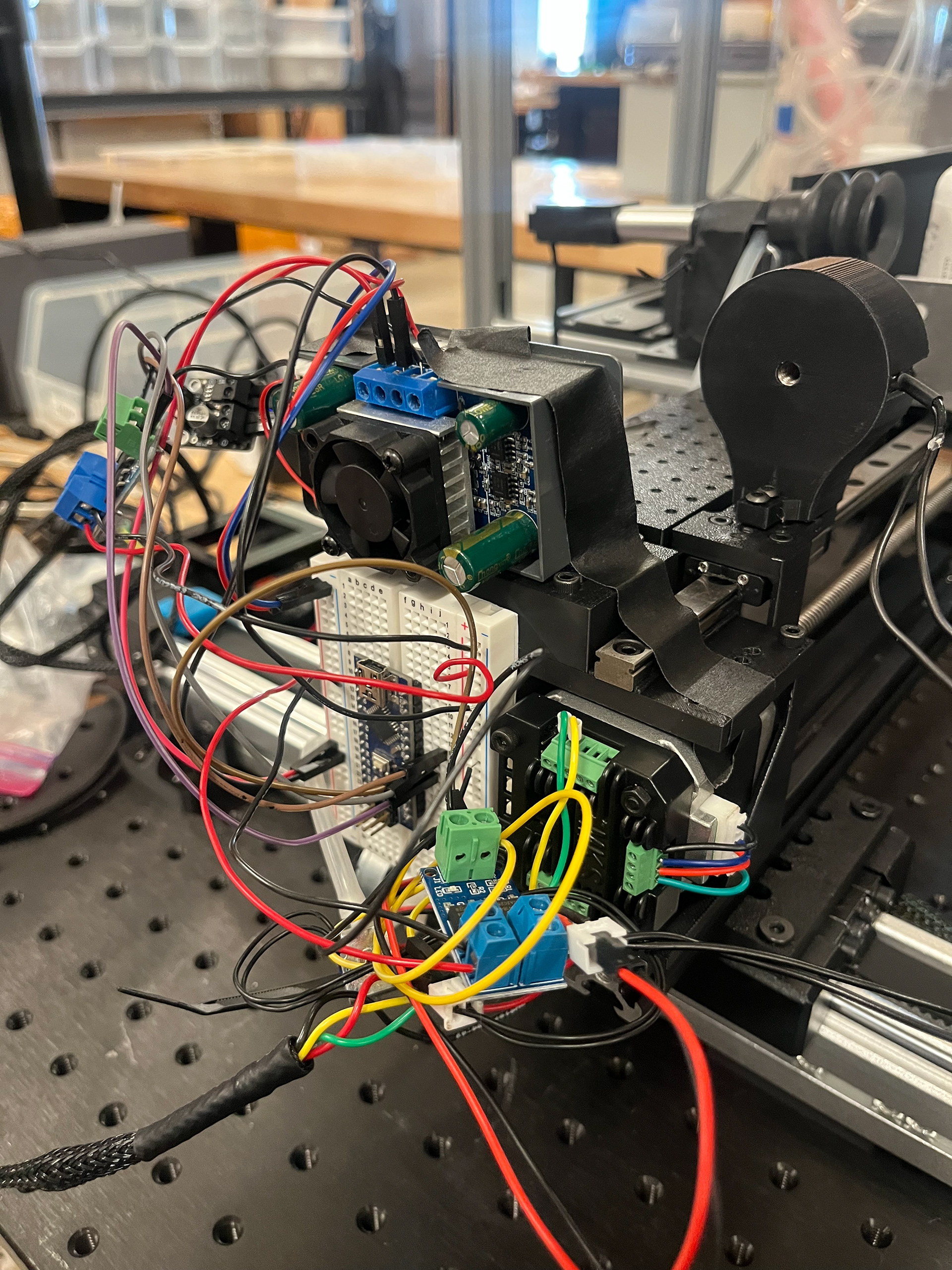